QUESTION: Why is it important for AG Tires to have small slip percentage to optimize traction, what is recommended % of slip for MFWD & 4WD Tractors, and how do tire physics and slip ratios differ from tracks?
AG Tire Talk Key Takeaways
GRI: “Operational efficiencies derived from managing tire slip are essential to minimizing costs as well as time and reducing soil compaction on your farm.”
YOKOHAMA: “Too much tire slip is inefficient—you’re spinning out, burning fuel on wheel movement that isn’t pushing your tractor forward. But too little slip is a problem, too. If you don’t experience a little slip, you are being inefficient in other ways. If your tires are encountering zero slip, it means they are in constant contact with all the resistance it takes to do the work…too heavily ballasted or that your tires are buried deep enough in the soil that they are having to constantly dig themselves out…”
PRECISION INFLATION: “The greatest Tractive Efficiency for tires occurs at a higher slip rate than rubber tracks. This is not a bad thing, just a result of different physics: TIRE sweet spot is between 6 to 12 % slip / TRACK sweet spot is 2 to 4 % slip. As tires have significantly fewer moving parts versus a complete track system, they are very efficient at higher slip ratios…for most applications this translates into more power to the ground for less cost, all with reduced soil compaction.”
BKT: “Although tracks work with less slippage, tests have shown that fuel consumption is adversely affected because of the need for higher horsepower motors to run tracks.”
MAXAM: “Tracks allow lower engine slip rates (down to 3%) due to the size of the track footprint when compared to radial tires operating at +8% slip rates; however, the weight of the tracked tractor components per axle and transmission system will consume more fuel and have a greater maintenance cost than a tire equipped tractor for the same field application.”
CONTINENTAL: “the looser the structure of the soil, the more slip required to generate high traction forces…the more lugs you have on the ground, the less slip you will require to generate the same traction force…”
MICHELIN: “VF Tire Technology…enables the tire to run at 40% less air pressure. The result is a very flat and elongated footprint allowing more lugs to contact the ground (increase traction) and significantly larger footprint area (reduce soil compaction). VF Tires due to less slip transfer more torque to the ground, saving up to 10% in fuel. Although slip ratio is lower in tracks, that does not necessarily mean they use less fuel, as more moving parts and increased machine weight results in more fuel burned in most applications.”
BKT USA, Inc.
David Paulk: Manager Field Technical Services
MFWD (Mechanical Front Wheel Drive) tractors are 4 WD tractors that can be locked in or out of 4-wheel drive. They have different sized drive tires on the front and rear and are geared to run at approximately the same revolutions. 4 WD tractors are full time 4-wheel drive. They are geared the same front to rear and run the same size tires on front and rear.
Ballast, air pressure, and tire slip go hand in hand when setting up a tractor. Ballast and air pressure should be used to achieve just enough traction to transmit power to the ground without excessive tire slip. Industry standards of 5% to 15% is the suggested range for tire slip. Industry standards suggest the ideal range is 8% to 12% for the least compaction, best traction, and fuel efficiency. If this is exceeded either way; it costs power from the tractor and fuel efficiency.
Having too much ballast and not enough air pressure can cause reduced tire slip under 5%. Too much ballast anchors the tires to the soil and allows too little tire slip. While this may sound like a good thing to have, it can cause tires to slip on the wheels, can cause lug cracking at the base of the lugs, and can cause drivetrain problems. When tires slip on the wheel, the rubber from the tire bead fills up the knurling in the wheel and will destroy the tire bead. Lug cracking at the base of the lug causes lugs to tear off because of the increased torque on the tire. Drivetrain problems can occur because there is too much stress on the axles and transmission. Tire slip provides a safety valve against shock overloads and reduces wear on the drivetrain. In sum, all of the above increases soil compaction and reduces the efficiency of the tractor- power and fuel are wasted in trying to move the tractor through the soil.
If slippage is lower than 5%, weights need to be removed and air pressures adjusted.
Having not enough ballast and too much air pressure can cause excessive tire slip above the 15% mark. The tires turn faster than the ground speed of the tractor. Too much slippage results in tire spin and energy loss to the ground. Less than 60%-70% of the power produced is used to pull an implement through the soil. This can drop to 50% in sandy soil. This causes tires to wear out prematurely and can cause lug cracking because of spinning. You are limited to the weight of the implements that can be pulled or carried. It adds to the fuel and labor cost.
If slippage is above the 15% mark, more weight may need to be added to the tractor and air pressures may need to be adjusted. Duals with reduced air pressures can help. If the old tires are heavily worn, new tires may be needed for the traction.
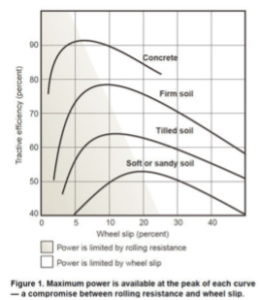
Best Slip = Peak Tractive Efficiency
The peak tractive efficiencies occur between 8% and 15% slip as shown on the 3 different types of soils. More power is lost to both rolling resistance and slippage in tilled soil versus no tilled soil. (Graph from Farm Energy, USDA, April 13, 2019)
Conversely, track tractors are made to operate with a 2% to 5% slip. They have a longer footprint and provide better flotation and traction in wet and muddy soil. Tracks are pulled through the soil while tires are pushed. Less slippage would be good, but there must be some slippage to protect the drive trains and the tracks from lug tearing and drive lug/guide lug tearing. Although tracks work with less slippage, tests have shown that fuel consumption is adversely affected because of the need for higher horsepower motors to run tracks. Track tractors are more expensive to buy and require more maintenance and upkeep.
Some amounts of slippage are important in both types of tractors to minimize damage to the tires and the tractor. This helps the tractors to perform to their potential with labor and fuel savings as well as minimizing damage to the soil.
Maxam Tire International
Greg W. Gilland: Business Development & Ag Segment Manager
As with all challenges in the Ag industry, every operation is a compromise between the equipment, the crop, the implement, and operational requirements to complete the job. In farming operations using either a 2WD, MFWD or 4WD Tractor, it is not recommended to use 100% of the rated axle power to pull your implement. If you use 100% of your power to pull an implement or load below 5 mph the farmer or grower runs the risk of over-straining the tractor engine and drivetrain systems causing premature wear of your components. This will also affect your tire life as well as possibly increasing soil compaction due to the additional strain. The goal is to achieve the optimal transmission of power to each axle allowing for percentage of tire slip to achieve the highest level of power and traction based on the load carried or pulled, road or field usage, and the required working speed to get the job done.
General Rules Related to Wheel & Tire Slippage:
- Too Much Slip = Loss of 25% to 30% of your transmitted power = more fuel consumed + increased tire wear with greater engine component use
- Too Little Slip = Too much weight (wheel weights, suitcase weight or liquid ballast) being pulled = Loss of efficiency + increased fuel consumption + increased soil compaction
- Zero (0) Slip = Only when “Roading” a tractor do you want the engine slip meter to drop to 0%.
Optimal Tractor Slip Percentage (%) Based on Tractor Type & Ground Working Conditions:
Tractor Type
- 2WD Tractors = from 10% up to 15% Slip Rate
- MFWD Tractors = from 8% up to 12% Slip Rate
- 4WD Tractors = from 8% up to 10% Slip Rate
Ground Working Conditions
- Hard Soils: Less Slippage for Maximum Engine Efficiency
- Soft Soils: More Slippage for Maximum Engine Efficiency
- Hard Surface Roads: 0% Slippage for Maximum Engine efficiency
Slip Defined
Tire or wheel slippage is a calculation that the tractor drive system measures by assessing the number of revolutions based on the tire circumference, power, time, and the actual distance traveled. In essence, if you travel 200 feet and your actual tire revolution (circumference) distance traveled is equal to 220 feet traveled your Wheel / Tire Slip rate = 10%. Example: 220 Tire Circumference Ft Traveled / 200 Actual Distance Traveled Ft = 10% Slip Rate
Factors that Can Impact Wheel / Tire Slippage
- Gear ratio considerations for MFWD Tractors: Ensure tires selected have the appropriate tire diameter Rear to front (RCI) to maintain the 5 to 1 engine gear ratio required for MFWD type tractors
- Employ the optimal tractor speed for any field work @ +5 mph to efficiently maximize engine power and transmission
- Set the Correct Tire Cold Inflation Pressure based on the actual axle Load (tire weight) and number of tires being employed by tire size.
- Employ the best weight distribution possible by adjusting the axle load ballast using suitcase weights, wheel mounted weights, or tire liquid ballast (not recommended) for the pulled or towed implement.
Recommended Ag Industry Tractor Weight Distribution by Axle Load
- 2WD Tractors Weight Distribution: 25-30% Front Axle & 75%-70% Rear Axle
- MFWD Tractors Weight Distribution: 40-45% Front Axle & 60%-55% Rear Axle
- 4WD Tractors Weight Distribution: 55-60% Front Axle & 45%-40% Rear Axle
In sum, all the above factors must be reviewed and employed as needed to ensure the optimal set up to achieve the best possible slip rate based on the tractor work and field conditions. The key always remains in understanding the load equation on your tires and the appropriate air pressure to carry that load. The right tire, at the right air pressure, with the right footprint or “gross flat plate” will deliver the optimal traction required and reduce your ground compaction impact.
Tires vs Tracks Difference
When we look at radial tires on tractors vs track systems, there are certain Ag industry general “assumptions” or rules that compare how tires and tracks are measured in the marketplace:
- Radial Ag tires operated at less than 18 PSI (1.2 Bar) generally have less ground compaction than tracks for the same field application = radial tires offer a better value
- Radial Ag tires operated above 18 PSI (1.2 Bar) up to +30 PSI (2.1 Bar) generally share almost equal ground contact pressure with tracks despite the longer track footprint contact area = radial tires offer an equal value to tracks
- When we look at self-propelled sprayers or large flotation / load applications (4WD Tractors, Floaters or Harvesters) that may be operating above +35 PSI (2.4 Bar) tracks will transmit less ground pressure due to their longer and/or wider contact footprint = tracks are offered only on harvesters & 4WD tractors.
- Tracks allow lower engine slip rates (down to 3%) due to the size of the track footprint when compared to radial tires operating at +8% slip rates, however the weight of the tracked tractor components per axle and transmission system will consume more fuel and have a greater maintenance cost than a tire equipped tractor for the same field application.
In summary, each application is different depending on the machinery selected, implements used, crop selection, soil conditions, and level of moisture impacting the use of tires vs. tracks. The farmer or grower must select the tool (tires or tracks) that best suits his need and fulfills his definition of value or return of investment to achieve his business objective.
GRI
Jim Enyart: Field Engineer – Sales
Low slip rates for Ag tractors directly correlate to higher efficiency. You don’t spend as much time spinning your wheels when you are trying to do an operation. The more you spin or slip, the more fuel you use on a per acre basis as well as increasing time, tire wear and soil compaction. Slip rates are affected by many factors including tractor size, horsepower, gross weight, weight distribution, drive train type, tire type and size, tread pattern, tread remaining, inflation pressures, number of tires, soil types, soil characteristics, soil moisture, temperature, speed, loads carried or pulled, depth of tillage as well as width and depth of operations, type of field operations and more! Each time you operate your tractor your slip rates change and need to be addressed to achieve tractive efficiency and manage costs.
The best thing to start with is making sure each tractor is set up properly. Ensure the gross weight is a minimum of 100# per horsepower and the weight distribution is correct for the type of drive system of the tractor. The slip meter will show you how the performance varies by operation as well as changing conditions. Try to maintain slip in the 8% to 15% range by adjusting the gear you are trying to pull with, the depth of a tillage operation or the width of your tillage implement if you can make adjustments.
Operational efficiencies derived from managing tire slip are essential to minimizing costs as well as time and reducing soil compaction on your farm.
Continental Agriculture North America
Dana Berger: Ag Business Development Manager at Continental Commercial Specialty Tires
Depending on how it’s used, the word ‘slip’ is often synonymous with less than desirable outcomes. To slip, is to slither, fall, skid, or misstep; therefore, you can conclude that a slip of a tractor tire is not usually a good thing. Each percent of slip translates to lost energy, which translates to increased demand on fuel and burning additional fuel means raising your operating costs. Add the growing fuel expense to another known fact; slippage harms the structure of the soil, and you’ll start to see a vicious cycle leading to lost profit levels. Lost profit will have you calculating all of the ways to reduce slip, as much as possible. There are two sides to every coin, though. Reducing your slip percentage, might be the ‘heads up’ approach, because you are attempting to combat the problem, before it occurs. But, as if to surprise you, the tail end of the coin throws a wrench in your plan because, slip is required to generate traction. Even in the best conditions, on a dry concrete surface, car tires require certain low slip rates to transmit acceleration and braking forces, as well as steering.
Making a general statement for optimal traction and slip rates on soil isn´t easy. Soil has a very wide range of surface types: dry sand without any structure, hard dry soils with some loose material and on up to a variety of wet, or even muddy forms. The following can be considered, with this in mind:
-the looser the structure of the soil, the more slip required to generate high traction forces
-the more lugs you have on the ground, the less slip you will require to generate the same traction force
A simplified overview for wheel tractor slip rates and pulling force can be seen in the diagram:
In very difficult weather conditions, slip rates can climb up to 40% or even more, but this is tolerable only for small/short passages of the total field. When working on dry soils, values of 10-15% percent are ideal, in more wet conditions, up to 20% can be acceptable for higher torque applications, like plowing, but less is if of course positive.
More ballast, up to a certain value, is helpful to reduce slip in high torque applications. It compresses loose material and generates a solid compacted base behind each lug. In combination with slip and with the friction coefficient, more ballast means a higher maximum force/torque being able to be transmitted. Even here, there are challenges. Too much ballast and your energy consumption increases to carry the additional load from the ballast, therefore, the risk of soil compaction increases, because more load means deeper track depth in wet soil.
Comparing Track Tractors versus Tire Tractors, in general the slip rates of tracks are lower to generate the same pulling force. With more lugs connecting the ground, the relative force per lug is lower, so this enables tracks to operate with generally lower slip rates for the same work. But are tracks always as a result, more efficient? No, not in any case, but there is a breakeven point where tracks start to be more efficient because the slip rates are generally lower. But, you need to consider that there is always some additional drag force required to turn all the parts of a track-system: rollers, centering lugs and rubber belts, that consumes extra power.
Think of walking barefoot on the beach, versus with shoes. Your toes certainly help get traction, but there is always a bit of a distorted footprint left behind from where your foot slid a bit to propel you forward. With a nicely treaded shoe, there is usually less visibility of a slip from your tread and your footprint is sustained. This works similarly with track tractors and tire tractors. Track tractors are like the shoe on the beach, in that they have a lower slip rate and more lugs (or tread) in contact with the ground, but you must also consider the sock that might slip off of your heel. A tractor with tires is like your barefoot, in that it will slip just a bit, but ultimately gets you down the beach just the same, with a few more calories burned.
Arguments can be made for tires having a lower slip rate, if you factor in a lower inflation pressure allowing the tire to lower an extra few lugs to the surface for grip and if the soil under the slightly slippery surface is dry. Tracks tend to slip through the surface mud and not grip the dry underneath, while tires will adapt and overcome with a deeper lug.
Michelin Ag
David Graden: Operational Market Manager – Agriculture
Desired slip percentages really depend on what the operator wants to achieve. Similarly, the type of tire fitted on the machine and air pressures ultimately affect target slip.
Let’s begin with tire design. In general, there are three different types of Ag tires: bias ply, standard radial, and IF/VF radials. Bias ply tires offer little in terms of footprint and the ability to adjust air pressures. Standard radial tires offer greater opportunity to adjust air pressures for larger footprints, in addition to carrying heavier loads. IF/VF radial technology offers the greatest opportunities to adjust air pressures, carrying capacity and tractive capacity.
Michelin invented VF technology in the early 2000’s by changing the casing design of an Ag tire to flex at a higher point in the sidewall, enabling the tire to run at 40% less air pressure. The result is a very flat and elongated footprint allowing more lugs to contact the ground (increase traction) and significantly larger footprint area (reduce soil compaction). VF Tires due to less slip transfer more torque to the ground, saving up to 10% in fuel.
Regardless of tire chosen, if an operator wants to maximize both fuel economy AND machine efficiency, they should target a slip rate of approximately 12%. At this slip rate, the operator is not using excess fuel to get the job done, while at the same time maximizing tractive efficiency. This is a calculated balance.
If an operator wants to maximize machine efficiency and is not as concerned about fuel costs, then I would recommend a slip rate between 7% and 9%. This is most common when fuel costs are low, as they have been for the prior past several years. At this slip rate, tractive capacity is at its best without creating power hop (assuming the machine’s weight distribution is optimized).
Due to the inherent mechanics difference of a track compared to a tire, slip rates of tracks are lower, in the range of 0% to 5%. Although slip ratio is lower in tracks, that does not necessarily mean they use less fuel, as more moving parts and increased machine weight results in more fuel burned in most applications.
In summary, if you own a track machine, your slip rate should vary between 0% and 5% and your fuel consumption should rise at a more constant rate as you demand more torque. If you own a MFWD or 4WD tire machine, the variables are more dynamic, enabling an operator to choose between maximum traction (7% to 9% slip ratio) or optimum traction & machine efficiency (~12% slip ratio).
Yokohama
Blaine Cox: National Product Manager–Agriculture, Golf & Turf
Slip is important in optimizing the efficiency of your tractor and protecting your drivetrain from strain and damage. Too much tire slip is inefficient—you’re spinning out, burning fuel on wheel movement that isn’t pushing your tractor forward (and you’re wearing down your tread too quickly).
But too little slip is a problem, too. If you don’t experience a little slip, you are being inefficient in other ways. Tires slip until they have accumulated enough resistance to push against so they can move your tractor forward and pull the load behind it, whether it’s a buggy full of grain or a field cultivator running through the soil. If your tires are encountering zero slip, it means they are in constant contact with all the resistance it takes to do the work. That’s an indication that you’re either too heavily ballasted or that your tires are buried deep enough in the soil that they are having to constantly dig themselves out, burning energy trying to overcome rolling resistance instead of just doing the necessary work of moving your tractor. (It also means they’re causing excessive soil compaction.)
The other problem with zero slip is that your drivetrain is under constant strain. Equipment manufacturers count on a little wheel slip as a way to absorb some of the energy that would otherwise wear on transmissions and other drivetrain components, much as tires absorb some of the impacts that would otherwise rattle equipment.
Optimum slip is…well, a little slippery. Like most things in farming, it depends on the soil, the conditions, and the machine. Optimum slip can range from 8 to 10% in firm soil—where we’d expect to feel less slip because the tires can encounter the needed resistance more quickly—to as high as 18 to 20% in really loose soil. Two-wheel-drive tractors tend to run optimally with a little more slip than 4WD tractors do, but the differences are pretty subtle: while a 4WD’s optimal range may be around 8 to 12% in average loam, average conditions, a 2WD tractor would be most efficient between 10 to 15% slip in the same field.
Slip occurs when the force applied to a tire exceeds its traction, so our high-traction tread patterns help reduce slip. You’ll see that in designs like our Stratified Layer Technology lugs on our Alliance Agri Star II R-1 radial, or in the hybrid block designs of our Alliance 550 and Alliance 363 radials. Yokohama Off-Highway Tires engineers also often work closely with OEMs to develop tires in step with farm equipment. Knowing the specifics of the machinery design helps us design tires that complement it very closely.
The bottom line is to embrace some slip—probably more than you think.
Precision Inflation Systems
Ken Brodbeck: VP of Technology
Tractors with tires and tractors with tracks are very different machines that operate at different levels of efficiency. The greatest Tractive Efficiency for tires occurs at a higher slip rate than rubber tracks. This is not a bad thing, just a result of different physics.
- For a tire, the sweet spot is between 6 to 12 % slip.
- For a track, the sweet spot is 2 to 4 % slip.
As the dashed lines in the graph show, the most efficient slip range for tires is 5 to 12% slip depending on soil type.
As tires have significantly fewer moving parts versus a complete track system, they are very efficient at higher slip ratios. For most applications this translates into more power to the ground for less cost, all with reduced soil compaction.
Why do Tracks Slip Less than Tires?
More Weight
A typical 400HP Four track machine weighs 10,000 lbs. heavier than it’s tire counterpart. More weight creates more drawbar pull. There is a reason tractor pulling contests have weight classes. More Weight = More Pull
For a comparison of traction, watch this tires vs. tracks pulloff. (20+) Facebook
Different Physics/Footprints:
Rubber tracks roll out a flexible but relatively stiff belt under the tractor. In soft conditions this minimizes the sinkage and rolling resistance. The drawback of the stiff rubber belt and all the support rollers is they take a large amount of power and fuel just to power the track. So, what you gain in not sinking into the soil, you give up in bending the belt around rollers creating more track rolling resistance, heated higher fuel burn.
In contrast, standard radial tires, especially when over inflated, create a short footprint and sink into the soil. This eats power and fuel.
With today’s new technology IF and VF tires, the footprints become longer without sinking. They become soft pneumatic tracks with footprints reaching 30 to 36” in length and very little rolling resistance.
Summary
In short, just because track machines have less slip does not necessarily mean they are more efficient at achieving desired drawbar pull with maximum fuel economy- and with a Central Tire Inflation System, only in rare circumstances will tracks outperform VF Tires set up at the optimum lowest field air pressure to carry the load.
As an example, most producers are running MFWD Tillage tractors at inflation pressures in the mid 20s, as they do not have a Central Tire Inflation System – clearly a situation where tracks will outperform.
The great news is, with Central Tire Inflation System and IF or VF tires, air pressure can often be reduced to mid-single digits, enabling tires to be more efficient at delivering optimum traction and reducing soil compaction compared to tracks, all with an equipment weight reduction of approximately 25% and $100,000 smaller price tag!
- To learn how PSI impacts soil compaction click here: https://agtiretalk.com/category/new-product/
All information is provided in this blog solely to provoke thought. All deductions made from information on this site must be confirmed by Certified Ag Tire Dealer before use. Ag Tire Talk does not recommend anyone conduct tire service work with exception of Certified Ag Tire Dealer Professionals.